We have overcome travel restrictions during the pandemic by working digitally to achieve the annual quality management certifications for our mills. Maintaining certifications is essential for us to continue supplying our customers. Therefore, we have turned to web conferencing and video calls in place of the usual in-person approach.
One example from April 2021 was when Lloyd’s Register completed its annual audit of the Quality Management System at Hofors using only digital meetings.
This process usually requires experts from the certification body to travel to our plants to inspect them before sitting down to review process steps and technical documentation such as quality processes.
However, international travel has been restricted by the COVID-19 pandemic so the Hofors team arranged multiple digital meetings and review of documentation and digital records over web conferencing.
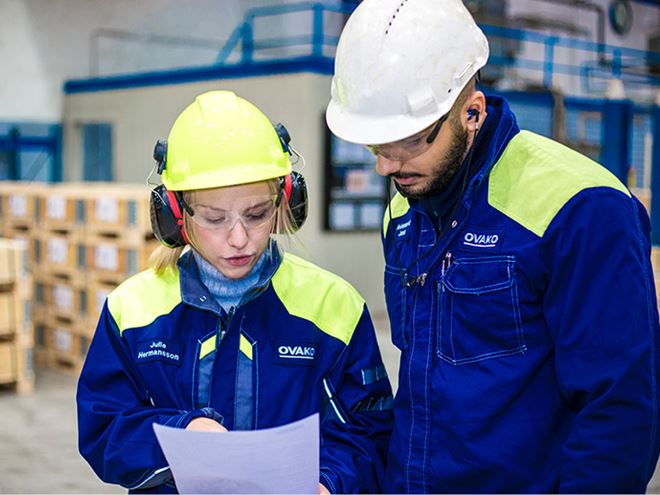
During the four-day process in April, auditors from Lloyd’s Register interviewed our team members online and discussed our approach to quality management in detail.
Mikael Karlsson, quality manager at Hofors, said: “Running the quality audit online was a new challenge and experience for us but is a prerequisite for our continued certification. Successfully passing the certification means that we can continue to supply customers that require it.
“The auditors only noted three minor deviations and none of a more serious nature, giving us a very good rating. We now have to rectify these points within 60 days before Lloyd’s Register will issue us with our new certificates.
“Passing the audit was a real team effort from team members at every level from operations to top management, as well as from employees who were directly involved and those supporting behind the scenes.”
A similar approach can be applied for other certification bodies, or customers, as long as they are satisfied that web conferencing gives them the right level of insight into our plants and production processes.
It’s also possible to use video calls to give visitors a virtual tour of our plants, as long as we are careful to share images only of areas of the plant that are not commercially sensitive or confidential.
Faster and more inclusive
Digital audits have huge time-saving potential. They take just a few hours in total. In comparison, each physical site visit takes a full day with safety briefings and breaks.
Typically, technical experts would need up to a week out of the office for an audit, taking account of flights, driving time between Stockholm airport and our mills, plus two or three nights in Sweden, and possibly also the effect of jet lag.
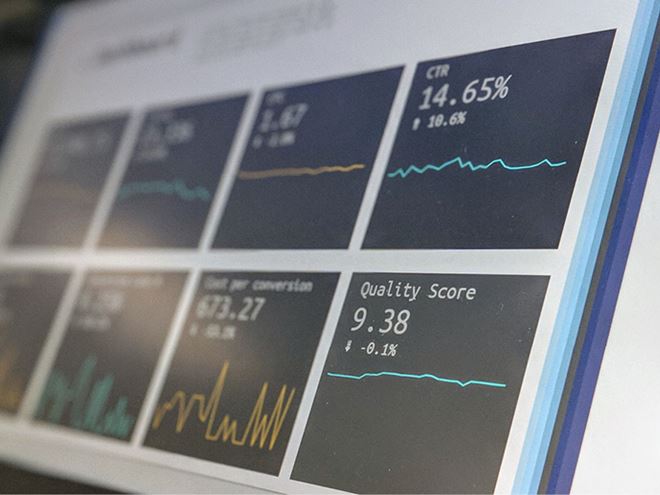
Mikael Thunman, technology and quality manager at Hällefors, said: “One unexpected outcome of the digital approach is that it is actually easier to communicate with our customer’s experts. It’s very noisy in the mill and we need to wear ear defenders so it can be very difficult to hear questions and answers. It’s ironic that I could hear them more clearly through an earpiece from thousands of kilometers away.”
Another benefit is that customers can send as many attendees as they want. In this way, an OEM or certification body can involve other members of its team to ask questions or learn from the experience of certifying a supplier.