Machinability of steel can have a big impact on the bottom line. By optimizing machine operations, a manufacturer can extend tool life, increase output and minimize waste.
Ideally, manufacturers want to find the ‘sweet spot’. This is the cutting speed that has the lowest cost when adding production and tooling costs. It is influenced by factors such as the workpiece material, the cutting tool’s design and material, and the machining parameters, such as cutting depth, feed and speed, etc. Material conditions such as heat treatment and metallurgical inclusions, as well as tool holding also play a role.
Chip control is central to machinability and manufacturers want short chips. These absorb heat and quickly clear away from the workpiece for undisturbed production, operator safety and a consistent tool life. They also enable faster speeds and longer tool life.
Steelmakers often add sulfur to improve the machinability of their steel and improve chip control. Sulfur reacts with non-metallic inclusions in the steel to form sulfides that are long and thin. These raise stress and encourage the formation of short chips.
However, the drawback is that sulfides can reduce fatigue performance, particularly when a component is loaded in the transverse direction.
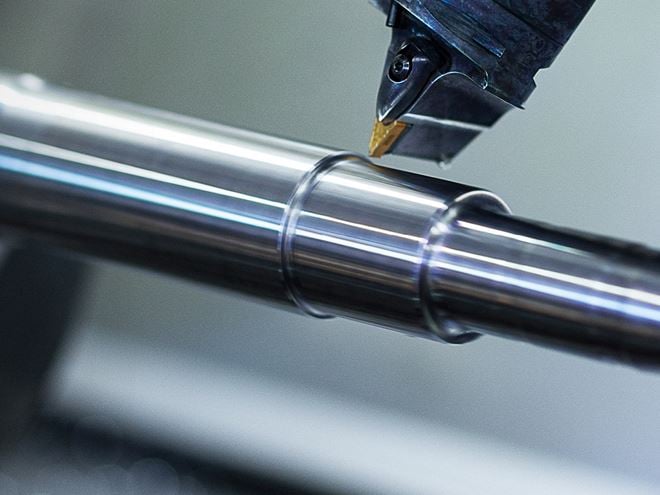
M for machinability
To counter this effect, Ovako has developed an additional treatment that focuses on precise control over steel at every step of production from raw material selection and the melt, to casting, hot rolling and final heat treatment.
It can be applied to any grade of steel and is called the M-Steel process, with M standing for machinability. It relies on the addition of minor elements into the steel melt to transform long sulfide inclusions into spherical particles.
The development dates back to the mid 1970s, when Raimo Karling, a metallurgist at the Imatra steel mill in Finland, carried out trials with the injection of calcium-silicon (CaSi) into the furnace. Not only did this improve the casting production but it significantly improved machinability.
The result is that some customers have reduced machining costs by up to 40 percent compared with conventional steel. That is thanks to higher machining speeds and also reduced tool wear, enabling cutting tools to last two or even three times as long.
At the same time, the process does not affect the steel’s hardenability and it even improves the fatigue strength and toughness.
Cutting costs and freeing capacity
One engineering subcontractor that is benefitting from M-Steel is Juhani Havisto of Finland. Its experts supply components to industrial customers in the pulp and paper, mining and process industries.
Havisto wanted to optimize its production of shafts, which had been a challenging process that required three steps and presented challenges in terms of straightness, vibration, tool wear and chip control.
Instead, they wanted to deploy a new machining center and robot. They found that by switching to M-Steel, it was able to increase cutting speed by 20 percent with fewer problems and extend tool life by a factor of five.
Considering machine, labor and tooling costs, the contractor was able to reduce the cost per piece by around a quarter from €134 to €101.30.
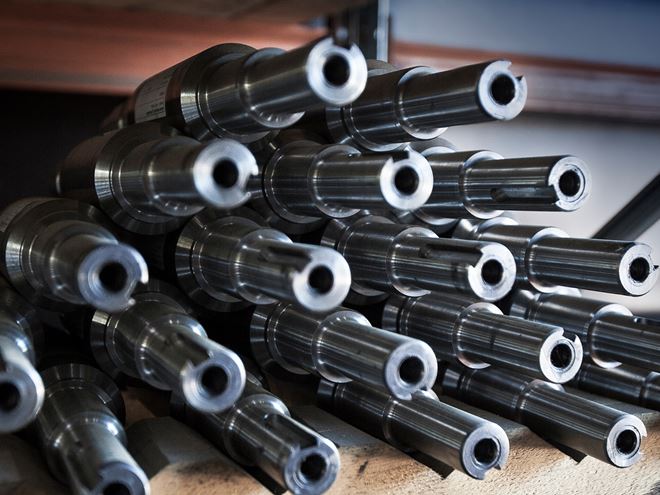
Spherical inclusions improve fatigue performance
M-Steel has a further benefit for fatigue performance due to the shape of the inclusions.
All inclusions act as microscopic stress-raisers. Over many thousands of loading cycles, they can become a focal point for cracks to form and eventually propagate through fatigue, causing the component to fail.
In standard steel, the long slender sulfide inclusions provide good fatigue performance when loading follows the longitudinal axis, parallel to the inclusions. However, transverse loading elevates the stresses, lowering the fatigue strength if a component is loaded across the direction of the inclusions.
In comparison, the spherical inclusions in M-Steel provide the same fatigue strength in both longitudinal and transverse directions.
This makes M-Steel suitable for components that will be exposed to moderate stress levels. However, engineers designing systems for high-stress applications can opt for bearing quality and isotropic quality steels, which have even fatigue higher performance.
Read our technical report on how M-Steel provides the mechanisms to improve steel machinability.