M-Steel® is a low alloyed, or non-alloyed, steel that is the ultimate choice when you need superior machinability combined with exceptional toughness and fatigue strength. It enables higher cutting speeds and improved productivity. Tests show that it can reduce machining costs by 30–40 percent. Manifold success stories with customer cases have shown more than doubled tool life when machining components from M-Steel, reducing the true cost per component.
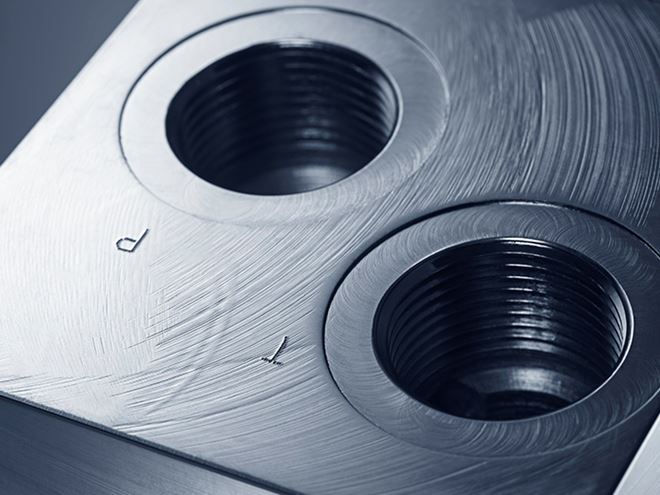
Reduced tool wear and increased productivity
In a highly competitive world, maximum utilization of machining equipment is of vital importance in order to minimize the time required to produce each single component. With cutting speeds up to 30 percent faster than conventional steel, M-Steel meets market demands for lower processing costs. In many circumstances the tool life span can be more than doubled when machining components from M-Steel. This not only saves on the actual machining time, but also reduces the true cost per component. Tool life and operational efficiency are also factors that have an impact on a business’s profitability. M-Steel has a consistent machinability from heat to heat, meaning that machines can be run with fixed high cutting rates and predictable tool change intervals from one production run to another. This makes them very suitable for un-manned production.
Advantages of M-Steel®
- Reduced machining costs and faster throughput by up to 30 percent
- Zero production interruptions, enabling un-manned production
- A deal-breaker in machining of pre-hardened quench and tempered steel products
- A deal breaker in both hard part turning with PCBN tools
- A deal breaker in grinding of carburized M-steel using CBN grinding wheels
- Very suited for multi-axially fatigue loaded components, thanks to spheroidized inclusions, as compared to standard steels.
The M-Steel concept
M-Steel treatment can be applied to any steel grade and any as-delivered condition. A rule of thumb is: the harder the machined steel, the more benefit you get with the M-steel. This means that hard quench and tempered M-steel 300-400 HB are very suitable to machine, as compared to standard steels.
The M-steel effect can be described as follows: Non-metallic inclusions are modified and controlled with calcium treatment. A protective layer, originating from these calcium inclusions, is deposited on the cutting tool during machining. The deposit reduces the chemical wear of the tool from the passing steel. It also acts as thermal barrier so that more heat goes with the chip and less heat flows into the cutting tool. Moreover, the hot chips curl more and thereby they display better chip breaking.
At every stage of the M-Steel production process, the material is optimized to improve machinability, from raw material through melting, casting, hot rolling and the final heat treatment. Individual delivery requirements can be met to supply your material in the best form for your machines in compliance with tight tolerances of straightness and dimension.
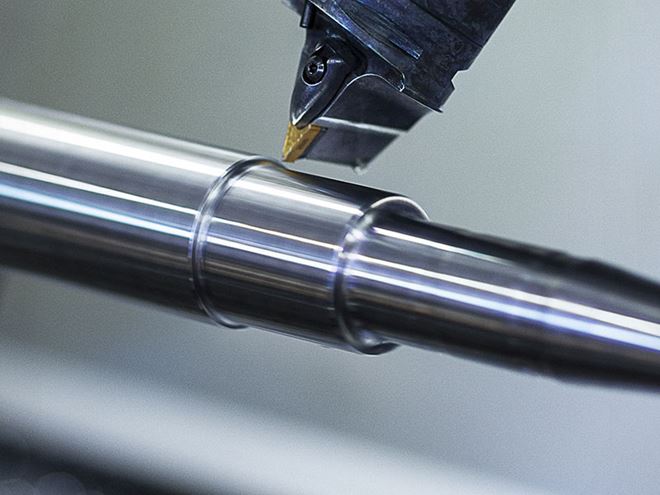
Increase cutting speed
The M-Steel effect is particularly pronounced in turning in very hard condition using Cubic Boron Nitride (PCBN) inserts. The cutting speed can be increased by 30 percent, leading to smoother component surface, at the same time as the tool life actually may increase by two times. Moreover, M-steels significantly reduces micro and macro chipping of the sensitive PCBN cutting edges. The same advantage can also be observed in hard grinding of M-steels with CBN grinding wheels. The material removal rate vs grinding wheel wear may be doubled with M-steel.
The M-steel metallurgy including calcium treatment also leads to spheroidized sulphides, meaning that the transversal properties in both toughness and fatigue strength are significantly improved as compared to the elongated MnS inclusions of standard steels. Thereby the M-Steels are very suited for multi-axially fatigue loaded applications.
We made it! But we are still not satisfied
What a journey! It took years of hard work to make our steelmaking operations more sustainable. In 2022, we went carbon neutral in all operations. But we´re still not satisfied - our journey continue for products with no CO2 emissions.
Read more about our path to carbon neutrality